Aircraft Structure
Classification of Aircraft
Aerostats
Aerostats are airborne vehicles that are made buoyant by using hot air or lighter gases. Their movement can be managed either by hand or remotely. These crafts are often utilized for recreational activities, advertising, and meteorological studies. Examples of aerostats include hot air balloons, airships, and weather balloons.
​
Aerodynes
Aerodynes refer to flying vehicles that are either propelled by their own thrust or introduced into the atmosphere through an external means. Examples of aerodynes include airplanes, helicopters, gliders, rockets, and missiles, which are frequently utilized for training, transportation, and military applications.

TYPES OF AIRCRAFT ACCORDING TO ENGINE

TYPES OF AIRCRAFT ACCORDING TO LOCATION & TYPE OF LANDING GEAR

TYPES OF AIRCRAFT ACCORDING TO WINGS
Parts of Aircraft
All aircraft, irrespective of their intended function, are comprised of the following fundamental components:
- Wings that lift
- Power plant that provides thrust
- Fuselage that accommodates the crew, passengers, cargo, fuel, and power plant
- unit consisting of fixed and movable surfaces for stabilizing the aircraft and adjusting its orientation in flight
- Landing gear
- Control system
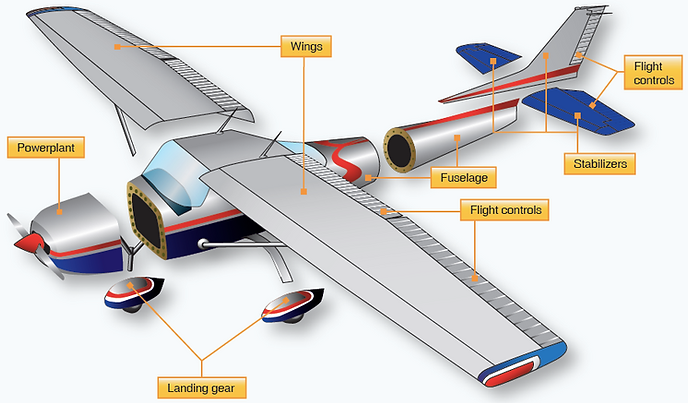
PARTS OF AN AIRCRAFT
Aircraft Structures
The airframe components fabricated from a diverse array of materials and are assembled using rivets, bolts, screws, welding, or adhesives. These aircraft components comprise various parts referred to as structural members, including stringers, longerons, ribs, and bulkheads.
Structural members are engineered to support loads and resist stress, often experiencing a combination of these forces. Generally they are designed to loads through tension or rather than bending.
In certain structures, strength may be the primary requirement, while others may necessitate different characteristics.
For example, components such as cowling and fairing are not typically required to withstand the stresses associated with flight or landing loads; however, they must exhibit attributes such as an aesthetically pleasing appearance and streamlined shapes.
Major Structural Stresses
In designing an aircraft, every square inch of wing and fuselage, every rib, spar, and even each metal fitting must be considered in relation to the physical characteristics of the metal of which it is made. Every part of the aircraft must be planned to carry the load to be imposed upon it. The determination of such loads is called stress analysis. Although planning the design is not the function of the aviation mechanic, it is, nevertheless, important to understand and appreciate the stresses involved in order to avoid changes in the original design through improper repairs.
​
The term “stress” is often used interchangeably with the word “strain.” Stress is an internal force of a substance which opposes or resists deformation. Strain is the deformation of a material or substance. Stress, the internal force, can cause strain.
There are five major stresses to which all aircraft are subjected.
-
Tension
-
Compression
-
Torsion
-
Shear
-
Bending
Tension
Tension is the stress that resists a force that tends to pull apart. The engine pulls the aircraft forward, but air resistance tries to hold it back. The result is tension, which tries to stretch the aircraft. The tensile strength of a material is measured in p.s.i. (pounds per square inch) and is calculated by dividing the load (in pounds) required to pull the material apart by its cross-sectional area (in square inches).
​
Compression
Compression is the stress that resists a crushing force. The compressive strength of a material is also measured in p.s.i. Compression is the stress that tends to shorten or squeeze aircraft parts.
​
Torsion
Torsion is the stress that produces twisting. While moving the aircraft forward, the engine also tends to twist it to one side, but other aircraft components hold it on course. Thus, torsion is created. The torsional strength of a material is its resistance to twisting or torque.
Shear
Shear is the stress that resists the force tending to cause one layer of a material to slide over an adjacent layer. Two riveted plates in tension subject the rivets to a shearing force. Usually, the shearing strength of a material is either equal to or less than its tensile or compressive strength. Aircraft parts, especially screws, bolts, and rivets, are often subject to a shearing force.
​
Bending
Bending stress is a combination of compression and tension. The rod has been shortened (compressed) inside of the bend and stretched on the outside of the bend.

TYPE OF STRESS ON AN AIRCRAFT
Fuselage
The fuselage is the main structure or body of the aircraft. It provides space, for cargo, controls, accessories, passengers, and other equipment. In single engine aircraft, it also houses the powerplant. In multi-engine aircraft the engines may either be in the fuselage, attached to the fuselage, or suspended from the wing structure. They vary principally in size and arrangement of the different compartments.
There are two general types of fuselage construction,
-
Truss Type
-
Monocoque Type
Truss type
A truss is a rigid framework made up of members such as beams, struts, and bars to resist deformation by applied loads. The truss-framed fuselage is generally covered with fabric.
​
The truss type fuselage frame is usually constructed of steel tubing welded together in such a manner that all members of the truss can carry both tension and compression loads. In some aircraft, principally the light, single-engine models, truss fuselage frames are constructed of aluminium alloy and may be riveted or bolted into one piece, with cross bracing achieved by using solid rods or tubes.

TRUSSEL TYPE FUSELAGE
Monocoque Type
The monocoque (single shell) fuselage relies largely on the strength of the skin or covering to carry the primary
stresses.
The design may be divided into three classes :
-
Monocoque
-
Semimonocoque
-
Reinforced Shell
The true monocoque construction uses formers, frame assemblies, and bulkheads to give shape to the fuselage, but the skin carries the primary stresses. Since no bracing members are present, the skin must be strong enough to keep the fuselage rigid. Thus, the biggest problem involved in monocoque construction is maintaining enough strength while keeping the weight within allowable limits.
​
To overcome the strength/weight problem of monocoque construction, a modification called semimonocoque construction was developed. In addition to formers, frame assemblies, and bulkheads, the semimonocoque construction has the skin reinforced by longitudinal members. The reinforced shell has the skin reinforced by a complete framework of structural members.
​
Different portions of the same fuselage may belong to any one of the three classes, but most aircraft are considered to be of semimonocoque type construction.

MONOCOQUE CONSTRUCTION
Semimonocoque Type
The semimonocoque fuselage is constructed primarily of the alloys of aluminium and magnesium, although steel and titanium are found in areas of high temperatures. Primary bending loads are taken by the longerons, which usually extend across several points of support. The longerons are supplemented by other longitudinal members, called stringers. Stringers are more numerous and lighter in weight than longerons. The vertical structural members are referred to as bulkheads, frames, and formers. The heaviest of these vertical members are located at intervals to carry concentrated loads and at points where fittings are used to attach other units, such as the wings, power plants, and stabilizers.
The stringers are smaller and lighter than longerons and serve as fill-ins. They have some rigidity, but are chiefly used for giving shape and for attachment of the skin. The strong, heavy longerons hold the bulkheads and formers, and these, in turn, hold the stringers. All of these joined together form a rigid fuselage framework. There is often little difference between some rings, frames, and formers. One manufacturer may call a brace a former, whereas another may call the same type of brace a ring or frame. Manufacturers’ instructions and specifications for a specific aircraft are the best guides.
​
Stringers and longerons prevent tension and compression from bending the fuselage. Stringers are usually of a one piece aluminium alloy construction, and are manufactured in a variety of shapes by casting, extrusion, or forming.
​
Longerons, like stringers, are usually made of aluminium alloy; however, they may be of either a one-piece or a built up construction. By themselves, the structural members discussed do not give strength to a fuselage. They must first be joined together by such connective devices as gussets, rivets, nuts and bolts, or metal screws. A gusset is a type of connecting bracket. The bracing between longerons is often referred to as web members. They may be installed vertically or diagonally.
​
The metal skin or covering is riveted to the longerons, bulkheads, and other structural members and carries part of the load. The fuselage skin thickness will vary with the load carried and the stresses sustained at a particular location.
There are a number of advantages in the use of the semimonocoque fuselage. The bulkheads, frames, stringers, and longerons facilitate the design and construction of a streamlined fuselage, and add to the strength and rigidity of the structure. The main advantage, however, lies in the fact that it does not depend on a few members for strength and rigidity. This means that a semimonocoque fuselage, because of its stressed skin construction, may withstand considerable damage and still be strong enough to hold together.
Fuselages are generally constructed in two or more sections. On small aircraft, they are generally made in two or three sections, while larger aircraft may be made up of as many as six sections. Quick access to the accessories and other equipment carried in the fuselage is provided for by numerous access doors, inspection plates, landing wheel wells, and other openings. Servicing diagrams showing the arrangement of equipment and location of access doors are supplied by the manufacturer in the aircraft maintenance manual.

SEMIMONOCOQUE CONSTRUCTION
Wing Configurations
Depending on the desired flight characteristics, wings are built in many shapes and sizes. In addition to the particular configuration of the leading and trailing edges, wings are also designed to provide certain desirable flight characteristics, such as greater lift, balance, or stability. Features of the wing will cause other variations in its design. The wing tip may be square, rounded, or even pointed.
Both the leading edge and the trailing edge of the wing may be straight or curved, or one edge may be straight and the other curved. In addition, one or both edges may be tapered so that the wing is narrower at the tip than at the root where it joins the fuselage. Many types of modern aircraft employ swept back wings.

DIFFERENT TYPES OF LEADING AND TRAILING EDGE OF A WING

DIFFERENT WING ATTACHMENT POINTS
Wing Structure
The wings of an aircraft are surfaces which are designed to produce lift when moved rapidly through the air. The particular design for any given aircraft depends on a number of factors, such as size, weight, use of the aircraft, desired speed in flight and at landing, and desired rate of climb. The wings of a fixed-wing aircraft are designated left and right, corresponding to the left and right sides of the operator when seated in the cockpit.
​
The main structural parts of a wing are
-
Spars
-
Ribs or Bulkheads
-
Stringers or Stiffeners
The wings of some aircraft are of cantilever design; that is, they are built so that no external bracing is needed. The skin is part of the wing structure and carries part of the wing stresses.
​
Other aircraft wings use external bracing (struts, wires, etc.) to assist in supporting the wing and carrying the aerodynamic and landing loads. Both aluminium alloy and magnesium alloy are used in wing construction.
The internal structure is made up of spars and stringers running span wise, and ribs and formers running chord wise (leading edge to trailing edge). The spars are the principal structural members of the wing. The skin is attached to the internal members and may carry part of the wing stresses. During flight, applied loads which are imposed on the wing structure are primarily on the skin. From the skin they are transmitted to the ribs and from the ribs to the spars. The spars support all distributed loads as well as concentrated weights, such as fuselage, landing gear, and (on multi-engine aircraft) the nacelles or pylons.
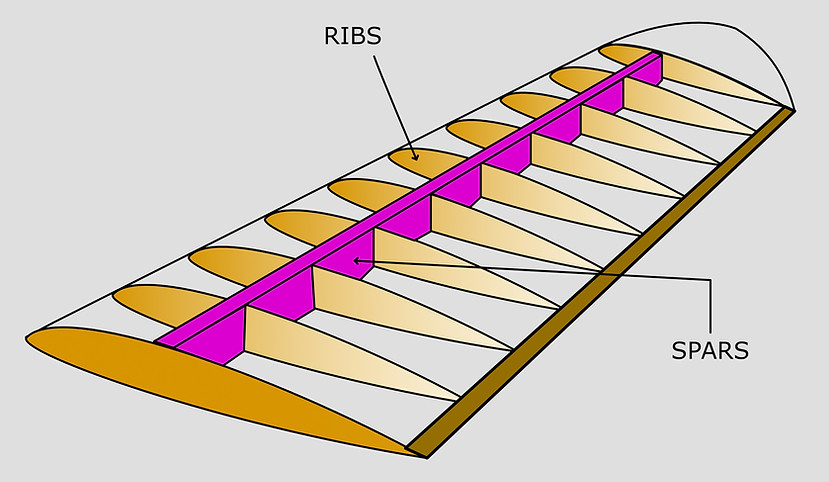
RIBS AND SPARS
The wing, like the fuselage, may be constructed in sections. One commonly used type is made up of a center
section with outer panels and wing tips. Another arrangement may have wing stubs as an integral part of the fuselage in place of the center section.
Inspection openings and access doors are provided, usually on the lower surfaces of the wing. Drain holes are also placed in the lower surface to provide for drainage of accumulated moisture or fluids. On some aircraft built-in walkways are provided on the areas where it is safe to walk or step. On some aircraft jacking points are provided on the underside of each wing.
Various points on the wing are located by station number. Wing station 0 (zero) is located at the center line of the fuselage, and all wing stations are measured outboard from that point, in inches.
Spars
Spars are the principal structural members of the wing. They correspond to the longerons of the fuselage. They
run parallel to the lateral axis, or towards the tip of the wing, and are usually attached to the fuselage by wing fittings, plain beams, or a truss system.
In general, wing construction is based on one of three fundamental design :
-
Monospar
-
Multi-Spar
-
Box Beam
The monospar wing incorporates only one main longitudinal member in its construction. Ribs or bulkheads supply the necessary contour or shape to the aerofoil. Although the strict monospar wing is not common, this type of design, modified by the addition of false spars or light shear webs along the trailing edge as support for the control surfaces, is sometimes used.
The multi-spar wing incorporates more than one main longitudinal member in its construction. To give the wing
contour, ribs or bulkheads are often included.
The box beam type of wing construction uses two main longitudinal members with connecting bulkheads to furnish additional strength and to give contour to the wing. A corrugated sheet may be placed between the bulkheads and the smooth outer skin so that the wing can better carry tension and compression loads. In some cases, heavy longitudinal stiffeners are substituted for the corrugated sheets. A combination of corrugated sheets on the upper surface of the wing and stiffeners on the lower surface is sometimes used.
​
Spars may be made of metal or wood depending on the design criteria of a specific aircraft. Most aircraft recently
manufactured use spars of solid extruded aluminium or short aluminium extrusions riveted together to form a spar.
The shape of most wooden spars is usually of the following shapes
-
The rectangular form, which can be either solid or laminated.
-
An I-beam spar that has been externally routed on both sides to reduce weight while retaining adequate strength.
-
A box spar, which is built up from plywood and solid spruce.
The I-beam spar, may be built up of wood or manufactured by an aluminium extrusion process. The I-beam construction for a spar usually consists of a web (a deep wall plate) and cap strips, which are extrusions or formed angles.
​​
The web forms the principal depth portion of the spar. Cap strips are extrusions, formed angles, or milled sections to which the web is attached. These members carry the loads caused by the wing bending and also provide a foundation for attaching the skin. Most metal spars are built up from extruded aluminium alloy sections, with riveted aluminium alloy web sections to provide extra strength.
The actual spar configuration may have either a plate or truss type web. The plate web consists of a solid plate with vertical stiffeners which increase the strength of the web. Some spar plate webs are constructed differently. Some have no stiffeners; others contain flanged holes for reducing weight.
​
A structure may be designed so as to be considered “fail-safe.” In other words, should one member of a complex structure fail, some other member would assume the load of the failed member.
A spar with “fail-safe” construction is made in two sections. The top section consists of a cap, riveted to the upper web plate. The lower section is a single extrusion, consisting of the lower cap and web plate. These two sections are spliced together to form the spar. If either section of this type of spar breaks, the other section can still carry the load, which is the “fail-safe” feature.
As a rule, a wing has two spars. One spar is usually located near the front of the wing, and the other about two thirds of the distance toward the wing’s trailing edge. Regardless of type, the spar is the most important part of the wing. When other structural members of the wing are placed under load, they pass most of the resulting stress on to the wing spars.
​
Wing Ribs
Ribs are the structural cross pieces that make up the framework of the wing. They usually extend from the wing leading edge to the rear spar or to the trailing edge of the wing. The ribs give the wing its cambered shape and transmit the load from the skin and stringers to the spars. Ribs are also used in ailerons, elevators, rudders, and stabilisers.
Ribs are manufactured from wood or metal are used with metal spars. Some typical wooden ribs, usually manufactured from spruce. The most common types of wooden ribs are the plywood web, the lightened plywood web, and the truss types. Of these three types, the truss type is the most efficient, but it lacks the simplicity of the other types.
​
A continuous gusset stiffens cap strips in the plane of the rib. This aids in preventing buckling and helps to obtain better rib/ skin glue joints where nail-gluing is used because such a rib can resist the driving force of nails better than the other types. Continuous gussets are more easily handled than the many small separate gussets otherwise required.
Various types of ribs are
-
Wing Rib or Pain Rib or Main Rib
-
Nose Ribs or False Rib
-
Butt Rib or Bulkhead Rib or Compression Rib
The wing rib, or plain rib, extends from the leading edge of the wing to the rear spar and in some cases to the trailing edge of the wing.
A nose rib is also called a false rib, extends from the wing leading edge to the front spar or slightly beyond.
The wing butt rib is normally the heavily stressed rib section at the inboard end of the wing near the attachment point to the fuselage. Depending on its location and method of attachment, a butt rib may be called a bulkhead rib or a compression rib, if it is designed to receive compression loads that tend to force the wing spars together.
Since the ribs are laterally weak, they are strengthened in some wings by tapes that woven above and below rib
sections to prevent side wise bending of the ribs.
Drag and anti drag wires are criss crossed between the spars to form a truss to resist forces acting on the wing in the direction of the wing chord. These tension wires are also referred to as tie rods. The wire designed to resist the back as tie rods. The wire designed to resist the backward forces is called a drag wire; the anti drag wire resists the forward forces in the chord direction.

TYPES OF RIBS
The wing is made up of spars, ribs, and lower and upper wing skin covering. With few exceptions, wings of this type are of the stressed skin design (the skin is part of the wing structure and carries part of the wing stresses).
The top and bottom wing skin covers are made up of several integrally stiffened sections. This type of wing
construction permits the installation of bladder-type fuel cells in the wings or is sealed to hold fuel without the usual fuel cells or tanks. A wing which is constructed to allow it to be used as a fuel cell or tank is referred to as a “wet-wing”.
A wing that uses a box-beam design type of construction not only increases strength and reduces weight, but it also enables the wing to serve as a fuel tank when properly sealed.
Both aluminium honeycomb and fiberglass honeycomb sandwich material are commonly used in the construction of wing and stabilizer surfaces, bulkheads, floors, control surfaces, and trim tabs.
Aluminium honeycomb material is made of aluminium foil honeycomb core, bonded between sheets of aluminium.
​
Fibreglass honeycomb material consists of fibreglass honeycomb core bonded between layers of fibreglass cloth.
In the construction of large aircraft structures, and in some small aircraft as well, the honeycomb sandwich structure employes either aluminium or reinforced plastic materials. Honeycomb panels are usually a lightweight cellular core sandwiched between two thin skins or facing materials such as aluminium, wood, or plastic.
Aircraft honeycomb material is manufactured in various shapes, but is usually of the constant thickness or tapered core types.
​
Wing Tip
The wing tip is often a removable unit, bolted to the outboard end of the wing panel. One reason for this is the vulnerability of the wing tips to damage, especially during ground handling and taxiing. The wing-tip assembly is of aluminium alloy construction.
​
The wing-tip cap is secured to the tip with countersunk screws and is secured to the inter spar structure at four points with 1/4 in bolts. The tip leading edge contains the best anti-icing duct. Wing-heated air is exhausted through a louver on the top surface of the tip. Wing position lights are located at the center of the tip and are not directly visible from the cockpit. As an indication that the wing tip light is operating, some wingtips are equipped with a lucid rod to transit the light to the leading edge.
Flight Control Surfaces
The directional control of a fixed-wing aircraft takes place around the lateral, longitudinal, and vertical axes by means of flight control surfaces. These control devices are hinged or movable surfaces through which the altitude of an aircraft is controlled during takeoff, flight, and landing. They are usually divided into two major groups, the primary or main, and the auxiliary control surfaces.
The primary group of flight control surfaces consists of ailerons, elevators, and rudders. Ailerons are attached to the trailing edge of both wings of an aircraft. Elevators are attached to the trailing edge of the horizontal stabilizer. The rudder is hinged to the trailing edge of the vertical stabilizer.
Primary control surfaces are similar in construction and vary only in size, shape, and methods of attachment. In
construction, control surfaces are similar to the all-metal wing. They are usually made of an aluminium alloy structure built around a single spar member or torque tube. Ribs are fitted to the spar at the leading and trailing edges and are joined together with a metal strip. The ribs, in many cases, are formed from flat sheet stock. They are seldom solid; more often, the formed, stamped out ribs are reduced in weight by holes which are punched in the metal.
The control surfaces of some aircraft are fabric covered. However, all turbojet powered aircraft have metal-covered surfaces for additional strength.
​
A control surface may serve a dual purpose, for example, one set of control surfaces, the elevons, combines the functions of both ailerons and elevators. Flaperons are ailerons which can also act as flaps. A movable horizontal tail section is a control surface which supplies the action of both the horizontal stabilizer and the elevators.
The secondary or auxiliary group of control surfaces consists of such members as trim tabs, balance tabs, servo tabs, flaps, spoilers, and leading edge devices.
Their purpose is to reduce the force required to actuate the primary controls, to trim and balance the aircraft in flight, to reduce landing speed or shorten the length of the landing roll, and to change the speed of the aircraft in flight. They are usually attached to, or recessed in, the main control surfaces.
Nacelles or Pods
Nacelles or pods are streamlined enclosures used on multi-engine aircraft primarily to house the engines. They are round or spherical in shape and are usually located above, below, or at the leading edge of the wing on multi-engine aircraft. If an aircraft has only one engine, it is usually mounted at the forward end of the fuselage, and the nacelle is the streamlined extension of the fuselage.
An engine nacelle or pod consists of skin, cowling, structural members, a firewall, and engine mounts. Skin and cowling cover the outside of the nacelle. Both are usually made of sheet aluminium alloy, stainless steel, magnesium, or titanium. Regardless of the material used, the skin is usually attached to the framework by rivets.
The framework usually consists of structural members similar to those of the fuselage. The framework includes
lengthwise members, such as longerons and stringers, and widthwise/vertical members, such as bulkheads, rings, and formers.
A nacelle or pod also contains a firewall which separates the engine compartment from the rest of the aircraft. This bulkhead is usually made of stainless steel sheet metal, or as in some aircraft, of titanium.
Another nacelle or pod member is the engine mount. The mount is usually attached to the firewall, and the engine is attached to the mount by nuts, bolts, and vibration absorbing rubber cushions or pads.
Engine mounts are designed to meet particular conditions of installation, such as the location and the method of attachment of the engine mount and the size, type, and characteristics of the engine it is intended to support. An engine mount is usually constructed as single unit which can be detached quickly and easily from the remaining structure.
Engine mounts are commonly made of welded chrome/molybdenum steel tubing, and forgings of chrome/nickel/molybdenum are used for the highly stressed fittings.
To reduce wind resistance during flight, the landing gear of most high-speed or large aircraft is retracted (drawn
up into streamlined enclosures). The part of the aircraft which receives or encloses the landing gear as it retracts is called a wheel well. In many instances, the wheel well is part of the nacelle; however, on some aircraft the landing gear retracts into the fuselage or wing.
​
Cowling
Cowling usually refers to the detachable covering of those areas into which access must be gained regularly, such as engines, accessory sections, and engine mount or firewall areas. Some large reciprocating engines are enclosed by “orange-peel” cowl panels. The cowl panels are attached to the firewall by mounts which also serve as hinges when the cowl is opened.
The lower cowl mounts are secured to the hinge brackets by pins which automatically lock in place, but can be removed by simply pulling on a ring. The side panels are held open by short rods; the top panel is held open by a longer rod, and the lower panel is restrained in the “open” position by a spring and cable.
All four panels are locked in the “closed” position by over centre steel latches. Which are secured in the closed position by spring-loaded safety catches. Cowl panels are generally of aluminium alloy construction; however, stainless steel is generally used as the inner skin aft of the power section, for cowl flaps and near the cowl flap openings, and for oil cooler ducts.
On turbojet engine installations, cowl panels are designed to provide a smooth airflow over the engines and to protect the engine from damage. The entire engine cowling system includes a nose cowl, upper and lower hinged removable cowl panels, and fixed cowl panel.
Empennage
The empennage is also called the tail section and most aircraft designs consist of a tail cone, fixed surfaces, and movable surfaces.
The tail cone serves to close and streamline the aft end of most fuselages. The cone is made up of structural members like those of the fuselage; however, cones are usually of lighter construction since they receive less stress than the fuselage.
Other components of the typical empennage are of heavier construction than the tail cone. These members include fixed surfaces that help steady the aircraft and movable surfaces that help too direct an aircraft’s flight. The fixed surfaces are the horizontal and vertical stabilisers. The movable surfaces are usually a rudder and elevators.
Stress in an empennage is also carried like stress in a wing. Bending, torsion, and shear, created by air loads, passes from one structural member to another. Each member absorbs some of the stress and passes the remainder to other members. The over load of stress eventually reaches the spars, which transmit it to the fuselage structure.
Landing Gear
The landing gear is the assembly that supports the aircraft during landing or while it is resting or moving about on the ground. The landing gear has shock struts to absorb the shock of landing and taxiing. By means of gear retraction mechanism, the landing gear attaches to the aircraft structure and enables the gear to extend and retract.
The landing gear arrangement either has a tail wheel or nose wheel. Landing gear arrangements having a nose
wheel are usually equipped for nose wheel steering.
Nose wheel aircraft are protected at the fuselage tail section with a tail skid or bumper. By means of wheels and tyres (or skis), the landing gear forms a stabilizing contact with the ground during landing and taxiing. Brakes installed in the wheels enable the aircraft to be slowed or stopped during movement on the ground.
Skin and Fairing
The smooth outer cover of the aircraft is referred to as skin. The skin covers the fuselage, wings, empennage,
nacelles, and pods. The material used for the skin covering is usually sheet aluminium alloy, treated so that it will not corrode. Magnesium and stainless steel may also be used to a limited extent. The thickness of the skin materials covering a structural unit may differ, depending on the load and stresses imposed within and throughout the structure.
To smooth out the airflow over the angles formed by the wings and other structural units with the fuselage, shaped and rounded panels or metal skin are attached. This panelling or skin is called fairing. Fairing is sometimes referred to as a fillet. Some fairing is removable to provide access to aircraft components, whereas other fairing is riveted to the aircraft structure.
Access and Inspection Doors
Access doors permit normal or emergency entrance into or exit from the aircraft. Also, they provide access to
servicing points and manually operated drains. Inspection doors provide access to a particular part of the aircraft being inspected or maintained. Access or inspection doors are either hinged or removable. They are fastened in the closed position with catch and locking mechanisms, screws, quick release devices, or cowling type fasteners.
Access and inspection doors that are removable often have a stencilled identification number that is identical to a number stencilled near the opening that they cover. Other access and inspection doors have a stencilled nomenclature to identify the opening that they cover.
Parts of an Helicopter
Helicopter airframe consist of
-
Fuselage,
-
Main rotor and related gearbox,
-
Tail rotor
-
Landing gear.

PARTS OF AN HELICOPTER
Helicopter Structure
Like the fuselages in fixed-wing aircraft, helicopter fuselages may be welded truss or some form of monocoque construction. Although their fuselage configurations may vary a great deal, most helicopter fuselages employ structural members similar to those used in fixed-wing aircraft. For example, most helicopters have such vertical / widthwise braces as bulkheads, formers, rings, and frames. They are also provided with such lengthwise braces as stringers and longerons. In addition, the gussets, joiners, and skin hold the other structural members together.
The basic body and tail boom sections of a typical helicopter are of conventional, all-metal, riveted structures incorporating formed aluminium alloy bulkheads, beams, channels, and stiffeners. Stressed skin panels may be either smooth or beaded. The firewall and engine deck are usually stainless steel. The tail boom is normally of semimonocoque construction, made up of formed aluminium bulkheads, extruded longerons, and skin panels or of welded tubular steel.
The members of a helicopter’s tail group vary widely, depending on the individual type and design. In this case, a stabilizer is mounted on a pylon to make up the group. In other cases, the stabilizer may be mounted on the helicopter tail cone or fuselage. In either case, both the pylon and stabilizer usually contain aluminium alloy structural members covered with magnesium alloy skin.
​
The types of structural members used, however, usually vary. A pylon usually has bulkheads, formers frames, stringers, and beams, making it somewhat of a blend of aircraft wing and fuselage structural members. The stabilizer is usually built more like an aircraft wing, with ribs and spars.
In a typical helicopter, the tail, body, and tail boom are constructed of all-metal stressed skin and metal reinforcing members. The helicopter cabin is normally a plexiglass enclosure which is supported by aluminium tubing in some models.
A large single-rotor helicopter is basically composed of two major sections, the cabin and the tail cone the cabin section is further divided into passenger or cargo compartments, which provide space for the crew, passengers, cargo, fuel and oil tanks, controls, and power plant. In multi-engine helicopters, the power plants are usually mounted in separate engine nacelles.
The aft section of a typical single-rotor helicopter consists of the tail cone, the fin, the tail-cone housing, the tail-rotor pylon, and the tail-end fairing. The tail cone is bolted to the rear of the forward section and supports the tail rotor, tail-rotor drive shafts, stabilizers, tail cone housing and tail-rotor pylon. The tail cone is of magnesium alloy and aluminium alloy construction. The tail-cone housing is bolted to the aft end of the tail cone. Trim stabilizers extend out on both sides of the tail cone forward of the housing.
Helicopter structural members are designed to carry a load or, stated differently, to resist stress. A single member of the helicopter structure may be subjected to a combination of stresses. In most cases it is desirable for structural members to carry end loads rather than side loads; that is, to be subjected to tension or compression rather than bending.
Structural members are usually combined into a truss to carry end loads. In a typical Pratt truss, the longitudinal and vertical members are tubes or rods capable of carrying compression loads.
Non structural members that are not removable from the helicopter are usually attached by riveting or spot welding.
Riveting is the most common method of attaching aluminium alloy sheets together. Parts that can be removed from the helicopter structure are usually bolted together.
Transparent materials are used for wind shields and windows and sometimes to cover parts requiring frequent visual inspection, Transparent plastic sheet and laminated glass are the materials most commonly used.
Some helicopter manufacturers use impregnated glass cloth laminate (fibber glass) as a lightweight substitute for certain metal parts, since fibber glass is simple to manufacture, has a high strength weight ratio, and resists corrosion.